The Ultimate Guide for Choosing Plasma Cutting Machine
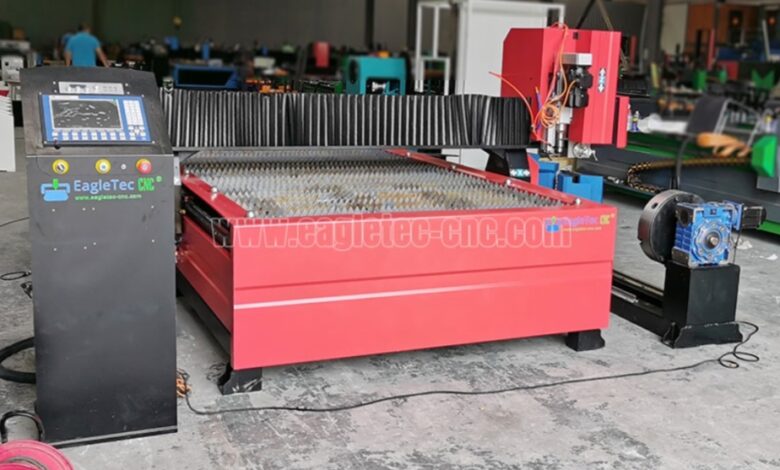
Plasma cutting is a technique that uses a high-temperature plasma arc to melt more or less (and melt) metal in a workpiece kerf and uses a faster plasma speed to remove molten metal to form and kerf.
A plasma cutting machine handles metal parts with the help of plasma cutting technology.
Industrial applications
Plasma cutting with different working gases can etch various intricate cutting, especially for non-ferrous metals (aluminum, stainless steel, copper, titanium, nickel). Oxygen-cutting methods are better.
The main advantage is that plasmas cuttings speed is faster if you cut metal of small thickness, especially in cutting ordinary carbon steel sheets. The rate can be 5-6 times faster than the method of cutting oxygen.
The cutting section is nice and clean, with minimal heat deformation and a low-heat-handling area.
Plasma cutting machine is broadly used in various fields such as automotive, locomotive, pressure vessel, chemical machine, nuclear industry, general machine, engineering machine, metal structure, ships, and more.
How to choose a cnc plasma cutting machine
Price
No matter what type of plasma is purchased, it is essential to consider the reason for the budget. If the budget is neglected, even if a fixed target can be achieved, it will not be possible to purchase if it exceeds the maximum budget.
Currently, plasma is mainly divided into two domestic and foreign groups, whose home price is divided into three, medium, and high three-quarters. Still, generally speaking, users should continue to be welcome!
The price of exports has risen several times over household goods, even more often, and consumables such as cutting nozzles and electrodes are more expensive!
In general, when compared to the exact definition of domestic plasma, out-of-the-world plasma cutting results are better; the disadvantage is that the cost and the delay in the use of the fee are too high, and public enterprises are difficult to accept!
Cutting the thickness
No matter how the type of plasma is used, it has its proper cutting edge. If the plasma energy is too high, it is not worth cutting thin plates! Usually, the plasma has a low capacity suitable for cutting thin plates, which are very popular.
Currently, 40-60a plasma cutting is mainly used for domestic metal plates less than 2mm, and exported is sometimes used, but the quantity is not significant because the price is high.
It is well worth mentioning that there are metal plates less than 2mm; it is essential to remember that other models, such as portable and gantry types, are not suitable for cutting other than the speed cnc plasma tables.
If it exceeds 2mm, it is not subject to this restriction and can be used. For thick steel plates, such as 2-16mm steel plates, portable and gantry-type equipment can be cut. Only the kind of grey is suitable if the thickness is 25 mm or more!
Cutting objects
Carbon steel is the most dependable method of cutting fire; whenever there is stainless steel, it must have plasma cutting machine! Otherwise, it cannot be cut by the flame! This master makes steel to repair all skilled craftsmen, using plasma cutting stainless steel and other alloy materials are its strength.
Read Also : Is Skateboarding a Good Way to Lose Weight?
Advantages of NC plasma cutting machine
It is better to cut the character
Scum, heat-damaging properties, high fillet, and cutting edge are the main factors affecting the cutting quality.
Especially in scum and heat that affects the area, plasma cutting is better than flame cutting. There is no residual scum on the cutting edge of the plasma, and the heat is involved in a tiny area.
Scum
The plasma process uses a gas-cooled gas to melt and blow the molten metal from the cutting surface.
Flames use chemicals to act between oxygen and cutting metal, producing iron-red slag or scum.
Due to the diversity of the technology, the scum produced by plasma cutting is small, and the attached scum is easy to remove. This scum can be dropped down quickly without grinding or removing, significantly reducing the time required for second processing.
Heat-damaged area
The heated area (haz) size is one of the most critical issues in cutting steel.
High temperatures alter the chemical structure of the metal, causing the hot edge to darken (burn color) and warp. If the hot edge is not removed, the workpiece may not be suitable for second welding. No matter which way to go, the sooner the flashlight moves, the smaller the hot touch area will be.
Due to the rapid cuttings of plasmas systems, heat affects a small area, which shortens the time spent in the second phase to remove heat waves.
Some flame cutters can also pay attention to the color of the fire. The hot, damaged area cannot be seen from the outside, but the color of the heat is not. In the same way, faster plasmas cuttings reduces the area of fire color.
High success
With cnc plasma cutting machine and punching running up to 8.5 times faster than flame cutting, the success rate can be significant, not counting the time saved in heat and secondary adjustment.
Low cost per unit
When evaluating costs, it is essential to understand the difference between operating costs per unit or meter.
So, why know the exact cost of cutting a part?
Running rate per meter is the cost of cutting per hour divided by full length (meters) that can be determined in one hour. Cutting costs include safe parts, electricity, gas, workforce, and maintenance costs.
Price per unit is the total length of cut needed to produce a fraction multiplied by the price per operating meter.